Development of galvanized coil production process
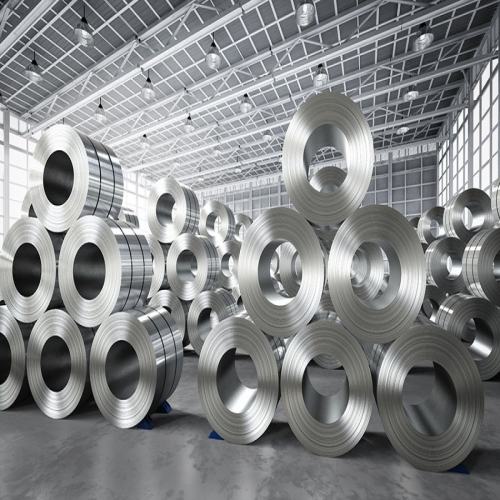
The evolution of galvanized coil manufacturing has been nothing short of transformative, fueled by the relentless pursuit of superior, durable, and cost-efficient steel products. At its core, galvanizing — the process of enveloping steel in a protective layer of zinc — significantly bolsters its resistance to corrosion. This enhancement renders galvanized steel ideal for a broad spectrum of industries, from towering construction projects to the sleek finishes of automotive designs and home appliances.
In the beginning, galvanizing was largely dominated by the hot-dip method, wherein steel coils were immersed in a bath of molten zinc. While effective, this approach was not without its drawbacks — most notably, issues with coating thickness and uniformity. However, as time marched on, significant innovations began to reshape the landscape. Continuous galvanizing lines, for example, ushered in an era of unparalleled precision, allowing manufacturers to control coating thickness with meticulous accuracy, resulting in products of superior quality.
Fast forward to today, and automation and cutting-edge digital control systems have become integral to galvanizing. These modern lines, now brimming with sensors, data analytics, and robotics, facilitate real-time adjustments, enabling the process to operate at higher speeds without compromising quality. Such technological advancements have not only ramped up efficiency but have also minimized energy consumption and waste, fostering a more sustainable and eco-friendly approach to manufacturing.
Looking ahead, the future of galvanized coil production appears boundless. As industries demand increasingly high-performance and environmentally conscious solutions, ongoing advancements in coating technology, material science, and automation promise to propel the industry into a new era of innovation and sustainability.