Choosing the right galvanized pipe is no mere task—it’s a pivotal decision that can make or break the durability and efficiency of your entire project. Whether you’re navigating the intricate requirements of construction, plumbing, or other industries that rely heavily on piping systems, selecting the right galvanized pipe is paramount. This guide delves deep into the process, offering crucial insights to help you make the most informed choice when it comes to galvanized pipes.
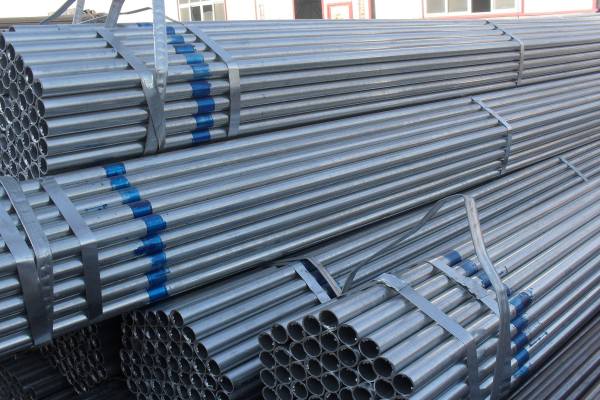
What Exactly is Galvanized Pipe?
At its core, a galvanized pipe is simply steel, but with a twist—it’s coated in zinc. This protective layer acts as a formidable shield, fighting against corrosion and rust. The galvanization process typically involves two main techniques: hot-dip galvanizing and electro-galvanizing. Both methods increase the pipe’s lifespan and resilience, but the choice between them hinges on the specific demands of your project. These pipes are indispensable in industries such as plumbing, construction, and manufacturing, where resistance to rust and corrosion is critical for maintaining system integrity.
Key Factors to Consider When Selecting Galvanized Pipe
- Pipe Size and Dimensions
Before anything else, the size of the pipe is an undeniable factor. Whether it’s for plumbing, irrigation, or industrial use, selecting the proper size ensures efficiency, proper flow, and pressure balance. A pipe that’s too large or too small can severely hamper performance. To get it right, consider the exact pressure requirements and flow rates needed for your system. Pay particular attention to the Nominal Pipe Size (NPS) as it directly correlates with the diameter, and ensure the wall thickness aligns with the pressure demands.
- Type of Galvanization Process
The galvanization process you choose plays a significant role in the pipe’s performance. The two predominant methods are:
Hot-dip Galvanizing: Here, the pipe is immersed in molten zinc, forming a thick, robust coating that delivers exceptional corrosion resistance. This method is particularly suited for high-demand environments, such as outdoor installations or applications exposed to harsh conditions.
Electro-galvanizing: Unlike hot-dip, electro-galvanizing applies zinc through an electric current, yielding a thinner, more uniform coating. While it offers a smoother finish, the corrosion protection may not be as formidable as that provided by the hot-dip method.
Consider the environmental conditions where the pipe will be placed. If your pipes will be exposed to extreme weather, chemicals, or high humidity, hot-dip galvanizing is likely your best bet.
- Material Quality
The quality of steel used in manufacturing galvanized pipes is another fundamental consideration. Galvanized pipes are commonly crafted from either carbon steel or mild steel. Carbon steel strikes a perfect balance between strength and affordability, making it a go-to option for many. Mild steel, on the other hand, offers superior flexibility and ease of installation but may not withstand certain types of wear and tear as effectively.
- Coating Thickness & Corrosion Resistance
A galvanized pipe’s corrosion resistance is determined largely by the thickness of its zinc coating. Thicker coatings provide better protection, particularly in environments where moisture, chemicals, or extreme weather are prevalent. When choosing pipes, consider whether the coating thickness meets ASTM standards like ASTM A53 or ASTM A123, which serve as industry benchmarks for durability and corrosion resistance.
- Expected Lifespan of the Pipes
Galvanized pipes, when properly installed and maintained, boast impressive service lives—often ranging from 30 to 70 years. But longevity isn’t just about the pipe’s inherent qualities; the environment and the specific application also play crucial roles. When budgeting for long-term infrastructure projects, consider investing in pipes with a thicker zinc coating and high-quality material to avoid costly replacements in the future.
- Specific Purpose & Application
The purpose of the pipes will shape your choices. Different industries demand distinct features from galvanized pipes:
Water & Sewage Systems: These systems require pipes that resist corrosion over prolonged periods of contact with water and waste. Galvanized pipes fit this need perfectly, providing a durable, long-lasting solution.
Oil & Gas Transportation: In these sectors, pipes must endure high pressure and hazardous conditions. Galvanized pipes offer the toughness needed to safely transport these volatile substances.
Agricultural Irrigation: The exposure to moisture, fertilizers, and chemicals in agricultural settings means galvanized pipes are often the material of choice due to their superior resistance to corrosion.
By aligning your pipe choice with the unique demands of your application, you’ll ensure optimal functionality and safety.