Understanding the Production Process of Aluminum Square Tubes
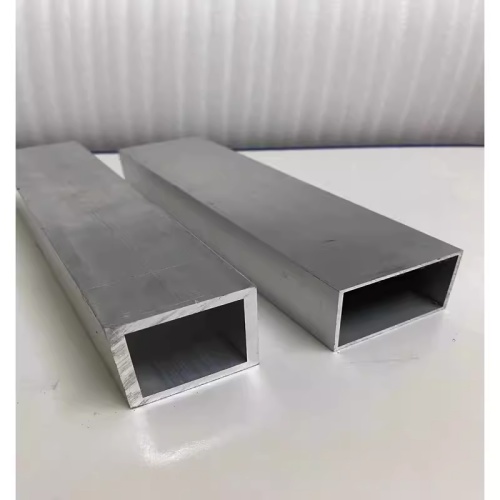
The creation of aluminum square tubes is a meticulous journey, shaped by a series of carefully orchestrated steps that culminate in the production of robust, lightweight, and highly durable components tailored for diverse uses. Let’s dive into the intricate process:
Material Selection
At the outset, a high-grade aluminum alloy—most commonly 6061 or 6063—is selected for its remarkable strength, superior corrosion resistance, and exceptional weldability. These alloys serve as the foundation, setting the stage for the tube’s overall performance.
Extrusion
The aluminum undergoes a heating process, transforming it into a pliable state before being relentlessly pushed through a custom-designed die. As the molten metal flows through, it is shaped into a continuous square tube, ensuring an even thickness and consistent strength across its entire length.
Cooling
As soon as the extrusion process is complete, the newly formed tube enters a cooling phase. This crucial step solidifies its shape and locks in its structural integrity, eliminating the possibility of any distortion or deformity.
Cutting
Once cooled, the long aluminum tube is sliced with precision. Exacting cutting tools are employed to sever the material into lengths that meet specific dimensional requirements, guaranteeing flawless sizing for each piece.
Surface Treatment
To bolster its resistance to the elements and elevate its appearance, the tube is subjected to surface treatments, with anodizing being a common choice. This process not only enhances corrosion resistance but also lends the tube a refined, aesthetically pleasing finish.
Quality Control
The final stage involves stringent quality assurance procedures. Each tube is rigorously tested, ensuring it adheres to the highest standards of strength, size, and visual quality, thus maintaining its reliability and excellence.
Aluminum square tubes, with their unmatched combination of performance and aesthetics, play a pivotal role across industries such as construction, automotive, and furniture, proving themselves as indispensable in a multitude of applications.